15 Precision Automation Trends Shaping the Future of the Semiconductor Industry
- AAAPlus Automation
- Jan 21
- 6 min read
The semiconductor industry is at a pivotal point, evolving rapidly with cutting-edge technology and trends that promise to redefine its future. Precision automation is at the forefront of this transformation, driving efficiency, quality, and innovation. In this article, we'll explore fifteen exciting trends that are shaping the landscape of semiconductor manufacturing through precision automation, making it easier for companies to adapt and thrive in an ever-changing market.
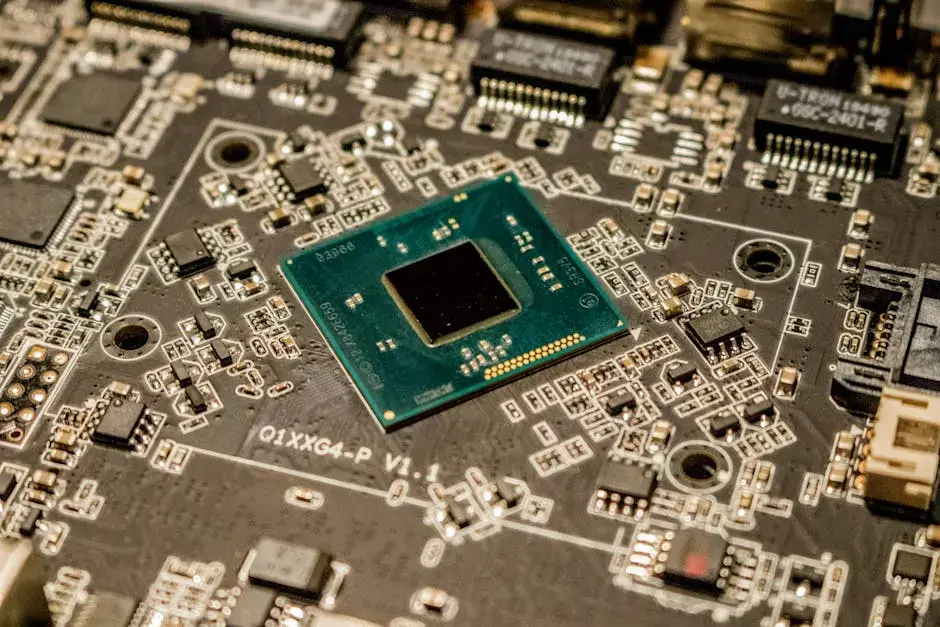
1. Smart Manufacturing Systems
Discover how smart manufacturing systems enhance productivity by integrating advanced data analytics and machine learning into the production process. By leveraging these technologies, manufacturers can monitor their operations in real time, identifying bottlenecks and inefficiencies as they occur. This level of insight allows for immediate adjustments, ensuring a smoother workflow and better resource utilization.
Moreover, these systems help track performance metrics that inform strategic decisions. For instance, with better visibility into production lines, facilities can predict yield rates and optimize schedules more effectively. This proactive approach not only boosts output but also supports continuous improvement initiatives, fostering a culture of excellence throughout the organization.
2. Collaborative Robots in Production
Learn about the rise of collaborative robots, or cobots, and how they are working alongside human workers to optimize efficiency and safety. Unlike traditional robots, cobots are designed to interact safely with humans, sharing the workspace without the need for safety cages. This integration enhances not only productivity but also employee morale.
In many semiconductor plants, cobots take on repetitive tasks, freeing human operators to focus on more complex and critical aspects of production. As this trend grows, we can expect to see a shift towards greater collaboration between machines and people—a dynamic that makes operations smoother and more effective. These robots are not just tools; they are partners in innovation.
3. Artificial Intelligence for Quality Control
Explore the deployment of AI in quality control processes, leading to better defect detection and enhanced product quality. With high-fidelity image analysis and pattern recognition capabilities, AI systems can pinpoint anomalies that human inspectors might miss. This increased precision not only reduces waste but also ensures that end products meet stringent industry standards.
By utilizing AI algorithms, manufacturers can also predict potential failures before they occur, enabling preventive measures that safeguard production lines. The continuous learning aspect of AI means that as more data becomes available, these systems become even more adept at identifying trends and predicting outcomes, driving quality assurance to new heights.
4. Predictive Maintenance Strategies
Understand how predictive maintenance powered by IoT technologies reduces downtime and maintenance costs by forecasting equipment failures. Traditional maintenance schedules can often result in either too much downtime—when machinery is in good condition—or emergency repairs—when issues arise unexpectedly. Predictive maintenance bridges this gap.
By analyzing data from sensors embedded in machinery, manufacturers can identify wear patterns and schedule maintenance before breaks occur. This strategic approach not only extends equipment lifespan but also contributes to a more reliable production process. Ultimately, this means greater efficiency and lower operational costs.
5. Digital Twins for Process Optimization
Unveil the concept of digital twins in semiconductor manufacturing and their role in simulating and optimizing production processes. A digital twin is a virtual representation of a physical asset, allowing manufacturers to test scenarios and gather insights without risking actual equipment. This capability is invaluable in refining processes and enhancing productivity.
With digital twins, engineers can experiment with different changes to production variables and immediately see the potential outcomes. This speeds up the optimization process significantly, enabling faster responses to market demands. Furthermore, as manufacturing systems evolve, digital twins facilitate a smooth transition by modeling adjustments before implementation.
6. Advanced Sensor Technologies
Dive into how advanced sensor technologies are revolutionizing monitoring processes, ensuring precision and accuracy in production. These sensors can continuously track a variety of parameters, from temperature to humidity, creating rich data streams that inform operational adjustments. The result is environmental conditions that are ideal for semiconductor fabrication.
Moreover, this influx of data can be analyzed to identify trends and anomalies, enabling proactive measures that enhance overall quality. Sensor technologies not only improve compliance with industry regulations but also offer manufacturers the ability to maintain consistency in product quality, regardless of fluctuations in the production environment.
7. Fully Automated Fabrication Plants
Examine the trend towards fully automated fabrication plants and what it means for the future of semiconductor production. The shift towards automation eliminates much of the variability introduced by human labor, offering a new level of consistency. These facilities utilize AI and robotics to streamline every aspect of production, from kit assembly to quality assurance.
The advantages of fully automated plants extend beyond efficiency— they also allow for better scalability and flexibility in production levels. Whether increasing output to meet booming demand or scaling back during quieter periods, automation offers manufacturing processes the ability to adjust operations without significant delays.
8. Edge Computing in Semiconductor Operations
Learn about the impact of edge computing on data processing and real-time decision-making in semiconductor operations. Rather than relying on cloud computing—which can introduce latency—edge computing processes data closer to the source. This enables instantaneous insights that can be acted upon immediately, enhancing operational responsiveness.
With edge computing, manufacturers can monitor critical parameters in real time, quickly responding to any deviations from the norm. This capability is particularly valuable in semiconductor production, where even slight variations can lead to significant quality issues. The result is a more agile manufacturing process that adapts seamlessly to changing conditions.
9. Integration of Blockchain Technology
Discover how blockchain technology enhances supply chain transparency and security in semiconductor manufacturing. By providing a decentralized ledger, blockchain ensures that all transactions are securely recorded and easily accessible. This transparency fosters trust among supply chain partners and can significantly reduce the risk of fraud.
In addition to security, blockchain allows for better traceability of materials and components. Understanding the origin of these elements is critical in an industry where quality and compliance are paramount. This integration supports responsible sourcing initiatives and can significantly improve brand reputation in the eyes of consumers and stakeholders alike.
10. Augmented Reality for Training and Maintenance
Explore the use of augmented reality to provide training for workers and assist in maintenance activities. AR offers immersive training experiences that can help new employees learn complex procedures faster and more effectively. Instead of relying solely on manuals, workers can visualize tasks and receive real-time guidance through AR interfaces.
During maintenance, technicians can use AR to overlay digital information onto physical equipment, showcasing relevant schematics and diagnostics. This reduces errors and enhances repair speed, minimizing downtime. In short, AR represents a significant leap forward in both workforce training and operational efficiency.
11. Enhanced Cybersecurity Measures
Understand the importance of robust cybersecurity measures as the semiconductor industry grows more reliant on connected technologies. With increasing connectivity comes the heightened risk of cyber threats that can compromise critical manufacturing processes and sensitive data. As a result, implementing cutting-edge security protocols is no longer optional; it’s essential.
These measures include everything from network segmentation to advanced threat detection systems. By fortifying their cyber defenses, semiconductor manufacturers can protect their operations and maintain the integrity of their products. In a world where digital breaches can lead to significant financial and reputational damage, prioritizing cybersecurity is crucial.
12. Custom Automation Solutions
Delve into the trend of custom automation solutions tailored to specific production needs, enhancing flexibility and efficiency. Off-the-shelf automation systems might not always meet the unique requirements of every semiconductor manufacturer. Custom solutions allow companies to address their particular challenges and operational quirks effectively.
These bespoke systems often incorporate advanced technologies that seamlessly integrate with existing infrastructure, leading to optimized workflows. By investing in tailored automation, companies position themselves to adapt quickly to technological advancements and shifting market demands.
13. Sustainable Manufacturing Practices
Learn how precision automation helps in adopting sustainable manufacturing practices while minimizing waste and energy consumption. By streamlining production processes and optimizing resource use, companies can significantly lower their environmental footprint. This responsible approach not only enhances operational efficiency but also aligns with growing consumer demand for sustainable products.
In addition, precision automation facilitates compliance with increasingly strict regulations surrounding environmental impact. By proactively addressing sustainability, manufacturers position themselves as leaders in the field, appealing to a marketplace that values environmental stewardship without compromising on quality.
14. Real-Time Data Analytics
Discover the power of real-time data analytics in driving continuous improvement in manufacturing processes and decision-making. With immediate access to analytics, managers can make informed decisions based on current data rather than relying on outdated reports. This agility allows for swift adjustments to production lines, enhancing overall efficiency.
Moreover, real-time insights facilitate predictive capabilities, enabling manufacturers to foresee challenges and address them proactively. As a result, companies can foster a culture of continuous improvement, where data-driven decisions lead to reduced waste and optimized operations.
15. Supply Chain Automation
Examine how supply chain automation transforms the way semiconductor companies manage inventory and logistics. By automating key supply chain processes, manufacturers can achieve unprecedented levels of accuracy and efficiency. Automated systems help track inventory levels in real time, ensuring that materials are available precisely when needed, reducing both excess stock and potential shortages.
Additionally, automation enhances communication and coordination across the supply chain. With integrated systems that provide visibility into every stage of production and delivery, companies can respond swiftly to market changes, improving their agility in meeting customer demands. The result is a more resilient and responsive supply chain.
Comments